Protecting hearing through collaboration, innovation and training
Posted by: Christian Moles
Posted on: 29/04/2022, 00:00
Protecting people from hearing loss at work is in the DNA of all our Eurosafe members, as we continuously investigate and suggest specific solutions, training or equipment that can be used to protect people from a whole range of hazards at work. With other personal protection equipment aimed at stopping more physical types of injury, protection of hearing is a much more long-term concern for businesses, especially those where employees are exposed to noise levels above 80 dB on a daily basis.
Our five key steps to protecting hearing include:
• Identification of noise levels in the workplace and specific applications
• Carrying out a hearing test based on noise data
• Selection of the right hearing protection equipment
• Training in the use, care and when to replace equipment
• Regular reviews of hearing validation and PPE equipment By testing noise levels across your operations and processes, you can understand which employees will be exposed to noise over 80 dB for any length of time.
You can also understand the types of noise and environment in which this noise is present. This enables you to match other PPE, like hard hats and safety goggles with relevant earmuff or earplug protection. Monitoring a worker’s hearing through routine testing is an effective way to identify any damage that may be the result of workplace noise. This is why Eurosafe members always suggest the use of hearing testing, not only to protect the employee, but to make sure the employer understands and documents the level of hearing capability of existing and importantly new employees.
Our five key steps to protecting hearing include:
• Identification of noise levels in the workplace and specific applications
• Carrying out a hearing test based on noise data
• Selection of the right hearing protection equipment
• Training in the use, care and when to replace equipment
• Regular reviews of hearing validation and PPE equipment By testing noise levels across your operations and processes, you can understand which employees will be exposed to noise over 80 dB for any length of time.
You can also understand the types of noise and environment in which this noise is present. This enables you to match other PPE, like hard hats and safety goggles with relevant earmuff or earplug protection. Monitoring a worker’s hearing through routine testing is an effective way to identify any damage that may be the result of workplace noise. This is why Eurosafe members always suggest the use of hearing testing, not only to protect the employee, but to make sure the employer understands and documents the level of hearing capability of existing and importantly new employees.
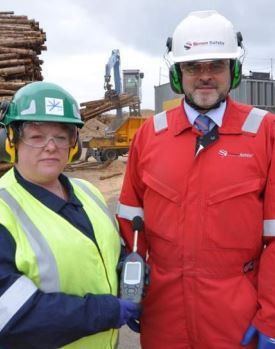
Through workplace noise monitoring you can then select the right hearing protection for each individual, working in each different high noise processes or areas. Typically, hearing validation systems have relied on subjectivity from the individual being tested. This works with a sound being played in a quiet environment and an individual who is wearing ear protection asked to indicate when they can hear the various pure tones of sound. Although it is a positive move from the employer to carry out hearing validation in the first place, using this subjective approach lacks clarity, can’t be measured and therefore recorded effectively. Not only does this put the end user at risk, it also has limited use in protecting the employer from future claims against hearing loss, whether that loss has occurred onsite or elsewhere.
With the new 3M™ E-A-Rfit™ Dual-Ear Validation system, based on science not subjectivity, these barriers to protecting hearing and safeguarding employees, as well as employers are removed, as the system works without any input from the employee.
The 3M™ E-A-R fit™ Dual-Ear Validation system is a lightweight kit that includes the hardware and accessories you need to perform the hearing validation testing, this includes:
• A speaker with a desk top stand
• Probed test earplug samples
• Two double-ended microphones (one for each ear)
• Power cable.
• USB connector to connect to a PC Additional 3M™ E-A-R fit™ Dual-Ear Validation system software is also provided for download from the cloud. This software enables the end user to record and safe data from each test, with an intuitive interface making usability simple.
With the new 3M™ E-A-Rfit™ Dual-Ear Validation system, based on science not subjectivity, these barriers to protecting hearing and safeguarding employees, as well as employers are removed, as the system works without any input from the employee.
The 3M™ E-A-R fit™ Dual-Ear Validation system is a lightweight kit that includes the hardware and accessories you need to perform the hearing validation testing, this includes:
• A speaker with a desk top stand
• Probed test earplug samples
• Two double-ended microphones (one for each ear)
• Power cable.
• USB connector to connect to a PC Additional 3M™ E-A-R fit™ Dual-Ear Validation system software is also provided for download from the cloud. This software enables the end user to record and safe data from each test, with an intuitive interface making usability simple.
Product List
For Simon Ashton, MD of Eurosafe member Simon Safety, the new 3M™ E-A-Rfit™ Dual-Ear Validation system represents the first time the business has been able to suggest a holistic approach to hearing, that also measures the impact other PPE can have on protecting the wearer from noise. Simon: “As both a consultant and provider of safety equipment, to a whole range of businesses working in diverse environments, we have a dual role to play in protecting individuals. This involves the assessment of the risks and the provision of different PPE options, that are fit for the purpose of protecting against these risks. “With hearing validation, you have two options, the in-ear plug and the outer ear defender, but as we know through our experience of dealing with numerous suppliers, there is a huge variance in both the performance, application and flexibility of products. This is not to mention how easy they are to maintain over time, particularly from a hygiene perspective. For example, we have seen ear defenders that have mould growing inside them.“When it comes to training, the 3M™ E-A-Rfit™ Dual-Ear Validation system really comes into its own, as it is vital that ear protection is fitted properly and also combined with the other PPE being worn for the job. For example, you may need different eye protection, as the use of glasses can potentially impact the seal of an ear defender.”
Eurosafe member Simon Safety and the PX Group, a leading integrated infrastructure solutions business, recently collaborated in a project with 3M. This was aimed at protecting employees and contractors working at the Western Wood Energy Plant at Port Talbot, Wales, a site operated and maintained by PX in consortium with Bilfinger Industrial Services. The power plant, owned by Western Bio-Energy Limited, generates enough electricity to power 10,000 homes, through the combustion of 160,000 tonnes of biomass per year. In order to do this, the plant shreds 80% virgin wood biomass material from sustainable forestry sources and up to 20% clean recycled wood biomass sourced from local suppliers. This material is fed into boilers, which in turn feed the onsite turbine, generating electricity. For PX Group it is the shredding, burning and generation phases of this process that create the most noise, which they need to protect employees from.
Having tested the equipment with Simon Safety staff that had been trained on the 3M™ E-A-Rfit™ Dual-Ear Validation system, PX opted to purchase it and train its own SHE team to carry out the regular testing and training. Michael: “We have now validated and trained all of our staff onsite and have made hearing validation a key part of our overall H&S reporting system, with plans for regular updates to ensure the training we have delivered is reinforced. “We are also validating contractors that come onto site to work in the areas where we have identified noise protection requirements. Having successfully implemented the system on the Western Wood Energy Plant we are now looking at rolling it out to other facilities with similar needs".
Eurosafe member Simon Safety and the PX Group, a leading integrated infrastructure solutions business, recently collaborated in a project with 3M. This was aimed at protecting employees and contractors working at the Western Wood Energy Plant at Port Talbot, Wales, a site operated and maintained by PX in consortium with Bilfinger Industrial Services. The power plant, owned by Western Bio-Energy Limited, generates enough electricity to power 10,000 homes, through the combustion of 160,000 tonnes of biomass per year. In order to do this, the plant shreds 80% virgin wood biomass material from sustainable forestry sources and up to 20% clean recycled wood biomass sourced from local suppliers. This material is fed into boilers, which in turn feed the onsite turbine, generating electricity. For PX Group it is the shredding, burning and generation phases of this process that create the most noise, which they need to protect employees from.
Having tested the equipment with Simon Safety staff that had been trained on the 3M™ E-A-Rfit™ Dual-Ear Validation system, PX opted to purchase it and train its own SHE team to carry out the regular testing and training. Michael: “We have now validated and trained all of our staff onsite and have made hearing validation a key part of our overall H&S reporting system, with plans for regular updates to ensure the training we have delivered is reinforced. “We are also validating contractors that come onto site to work in the areas where we have identified noise protection requirements. Having successfully implemented the system on the Western Wood Energy Plant we are now looking at rolling it out to other facilities with similar needs".